Profesjonalne wsparcie geotechniczne
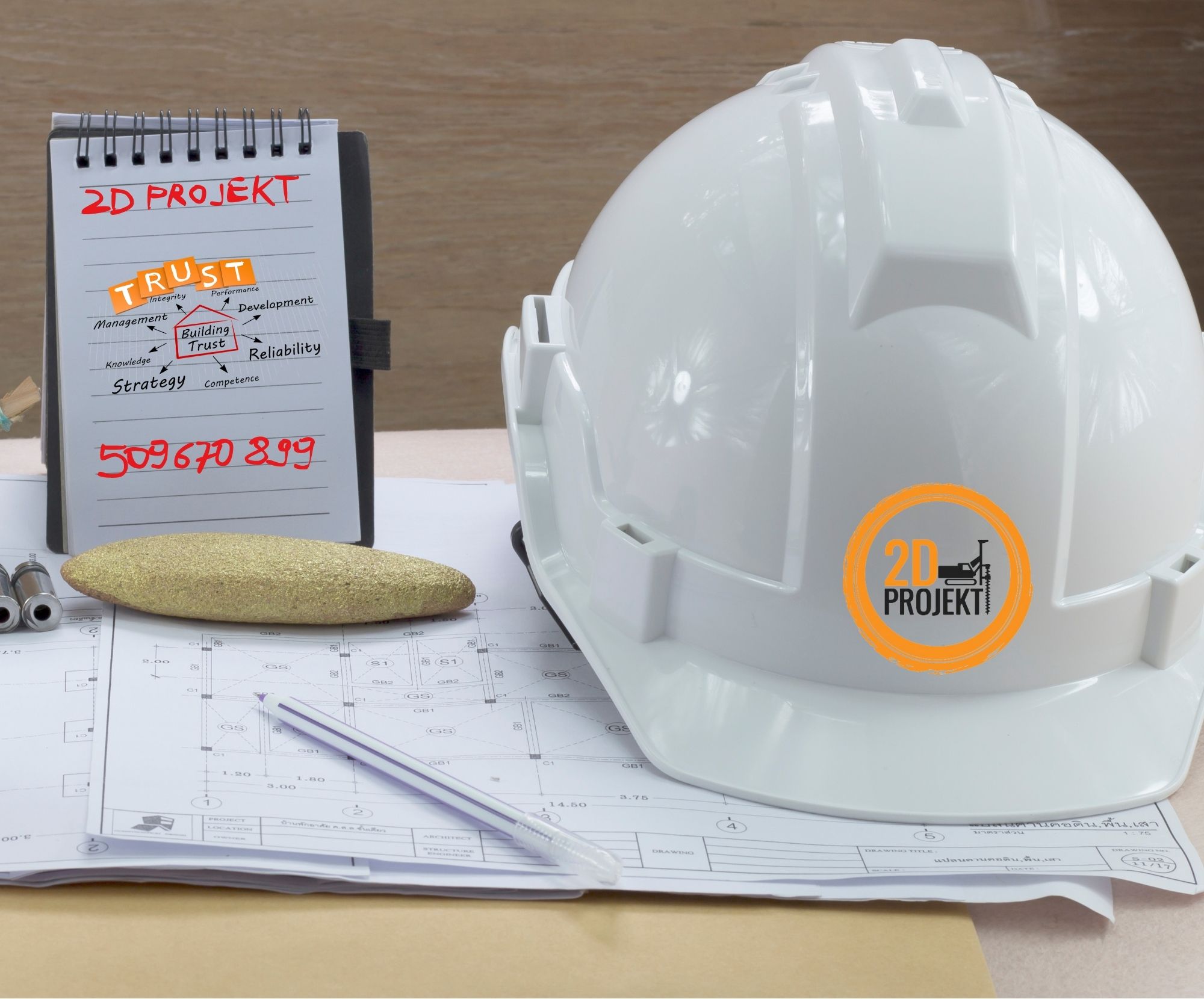
Projekty wykonawcze przekroczeń
bezwykopowych
Projektujemy kompleksowo przekroczenia bezwykopowe które umożliwiają pokonywanie przeszkód na drodze projektowanych instalacji np. rzek, zabudowy czy terenów pod ochroną. Specjalizujemy się w projektowaniu dużych przekroczeń w technologiach: mikrotunelowania, Direct Pipe oraz horyzontalnych przewiertów sterowanych (HDD).
2D PROJEKT specjalizuje się w projektowaniu dużych i trudnych przekroczeń bezwykopowych. Wykonujemy także analizy wytężenia rur przewiertowych/osłonowych zarówno w fazie instalacji jak i eksploatacji.
Potrzebujesz wsparcia w projektowaniu geotechnicznym?
Napisz lub zadzwoń i uzyskaj fachową pomoc.
Najczęstsze pytania
Czym jest projekt wykonawczy i technologiczny w zakresie przekroczeń bezwykopowych?
Dokumentacja projektowa w stadium wykonawczym i technologicznym to dokumentacja która jest bezpośrednio używana na placu budowy. Są do dokumentacje o najwyższej szczegółowości. Przeważnie zawierają część opisową, część obliczeniową i bardzo szczegółowe rysunki.
Projekty na etapie realizacji prac opieramy na analizie ekonomicznej, możliwościach technologicznych Wykonawców i wieloletnim doświadczeniu w projektowaniu oraz optymalizacji przekroczeń bezwykopowych.
Jakie technologie bezwykopowe są dostępne na polskim rynku budowlanym?
W przypadku konieczności zaprojektowania i wykonania przekroczenia bezwykopowego np. w ramach projektowanej sieci gazociągowej, światłowodowej, wodociągowej itp. można wykorzystać takie technologie jak:
- Mikrotunelowanie (Mikrotuneling)
- HDD
- Direct Pipe
- Przeciski pneumatyczne (wbijanie rur stalowych) – Pipe-jacking
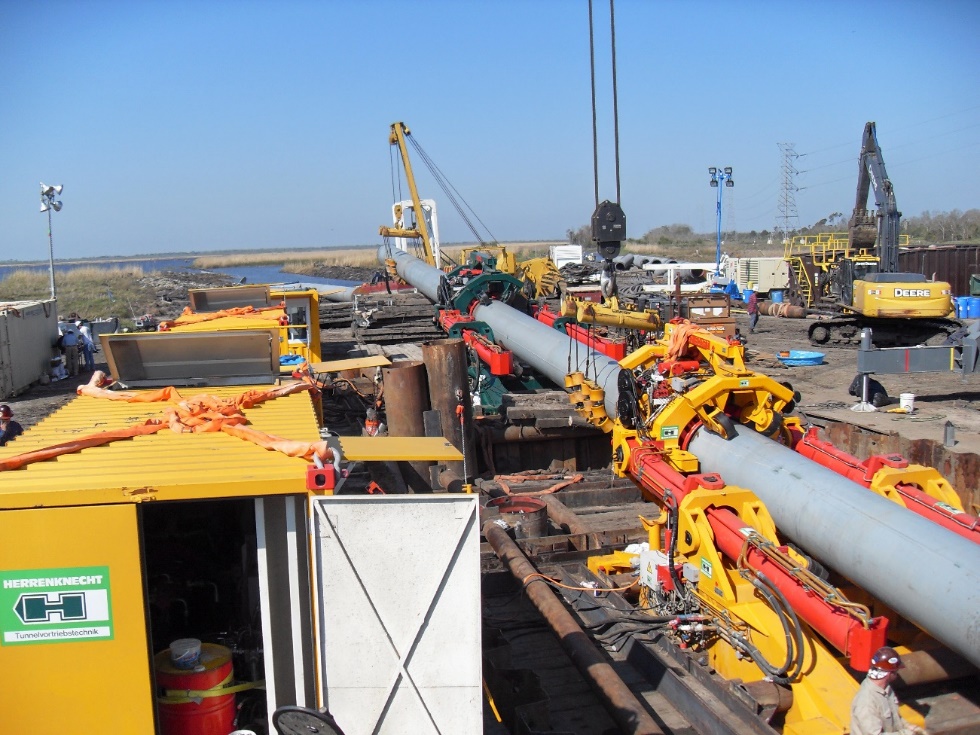
Jakie najczęściej przeszkody terenowe są pokonywane metodami bezwykopowymi?
Najczęściej metody bezwykopowe są stosowane do przekraczania takich przeszkód terenowych jak rzeki, kanały wodne, autostrady, drogi, tory kolejowe oraz zbiorniki wodne, bagna i wszelkie obszary chronione. Generalnie obszary gdzie nie jest możliwe wykonanie wykopu otwartego lub gdzie nie ma to ekonomicznego uzasadnienia.
Na czym polega metoda mikrotunelowania?
- Mikrotunelowanie — to jednoetapowa, wysoce zautomatyzowana metoda pokonywania przeszkód terenowych. Technologia ta polega na drążeniu tunelu przy pomocy tarczy skrawającej z jednoczesnym przeciskaniem rur przewodowych/osłonowych. Tarcza ta umieszczona jest na czole urządzenia do mikrotunelowania, zwanego również głowicą. Wbudowywanie rurociągu w tej technologii odbywa się od wykopu początkowego do docelowego. W wykopie początkowym, zwanym również komorą startową lub szybem startowym, umieszczona jest główna stacja przeciskowa, składająca się siłowników hydraulicznych, pierścienia wciskającego oraz płyty kotwiącej. Na specjalnych prowadnicach zwanych łożem, ułożonych również w wykopie początkowym, umieszcza się urządzenie do mikrotunelowania. Urządzenie to jest wciskane w grunt przy pomocy głównej stacji przeciskowej. W tylnej części wykopu początkowego wbudowany jest betonowy lub żelbetowy blok oporowy, o który rozpierają się siłowniki hydrauliczne. Jego zadaniem jest przejęcie sił reakcji od siłowników hydraulicznych i przekazanie ich na grunt. Główna stacja przeciskowa jest kotwiona do bloku oporowego za pomocą płyty kotwiącej. Bezpośrednio za wciskaną w grunt głowicą do mikrotunelowania przeciskane są rury. W trakcie wykonywania przekroczenia dokładane są kolejne rury mikrotunelowe. Wewnątrz wbudowywanego rurociągu prowadzonych jest wiele przewodów, między innymi przewody płuczkowe zasilające, przewody transportujące urobek, kable zasilające, przewody transmisji danych, przewody systemu smarowania, przewody hydrauliczne oraz inne. Przy każdorazowym dokładaniu kolejnego odcinka rury, przewody te muszą być rozłączone, przeciągnięte przez dokładaną rurę a następnie ponownie połączone.W czasie wykonywania przekroczenia tarcza skrawająca urabia grunt na przodku. Odspojony grunt dostaje się do komory kruszenia, w której przy pomocy kruszarki stożkowej jest rozdrabniany, a większe kamienie kruszone. Urobek transportowany jest przy pomocy przenośników ślimakowych, podciśnienia (system pneumatyczny) lub po zmieszaniu z wodą przewodami tzw. systemem płuczkowym zamkniętym.W skład systemu do mikrotunelowania wchodzą:
- urządzenie do mikrotunelowania składające się zazwyczaj z trzech segmentów oraz tarczy wiertniczej,
- główna stacja przeciskowa,
- kontener sterowniczy, znajdujący się w bliskim sąsiedztwie wykopu początkowego; system sterowania i kontroli, w którego skład wchodzą w przypadku najczęściej stosowanego systemu laserowego: laser kierunkowy, elektroniczny odbiornik wiązki laserowej, siłowniki hydrauliczne służące do sterowania głowicą mikrotunelową oraz stanowisko operatora (wiertacza);
- system przygotowania i oczyszczania płynu wiertniczego (najczęściej o budowie kontenerowej) z sitami do separacji grawitacyjnej urobku, sitami wibracyjnymi oraz hydrocyklonami i wirówkami;
- system smarowania zewnętrznych powierzchni przeciskanych rur, obejmujący mieszalnik cieczy smarującej, zbiornik, pompę, węże tłoczące, rozdzielacze i dysze;
- rury mikrotunelowe
Pozostałe elementy zestawu mikrotunelowego to: agregaty prądotwórcze i hydrauliczne zabudowane najczęściej w kontenerze, służące do zasilania, między innymi pomp płuczkowych, głównej stacji siłowników hydraulicznych, stacji pośrednich, silników hydraulicznych i innych urządzeń; pompy płuczkowe (pompa zasilająca podająca czystą płuczkę, zamontowana na powierzchni terenu, pompa tłocząca umieszczona w urządzeniu do mikrotunelowania oraz pompa tłocząca zamontowana w wykopie początkowym); wyposażenie pomocnicze takie jak: rurowe przewody płuczkowe z szybkozłączami, urządzenia do pomiaru wydatku płuczki, przewody zasilające, przesyłowe i inne.
Głównym elementem systemu do mikrotunelowania jest głowica. Składa się zazwyczaj z trzech, segmentów (modułów). W pierwszym module znajduje się tarcza urabiająca grunt, komora kruszenia z kruszarką stożkową, łożysko główne wraz z silnikiem napędzającym je. W pozostałych modułach znajdują się między innymi siłowniki hydrauliczne, służące do sterowania głowicą oraz elektroniczny odbiornik wiązki laserowej.
Tarcza urabiająca grunt napędzana jest silnikiem hydraulicznym lub elektrycznym poprzez łożysko główne, obracając się skrawa grunt. Odspojony urobek przedostaje się do komory kruszenia, gdzie jest rozdrabniany w kruszarce stożkowej. Kruszarka taka pozwala na rozdrabnianie kamieni o wielkości nawet do 30% średnicy urządzenia.
W systemach, w których urobek transportowany jest przy pomocy płuczki, do komory kruszenia podawany jest poprzez specjalne dysze płyn wiertniczy, najczęściej w postaci płuczki bentonitowej. Płuczka ta miesza się z urobkiem i jest zasysana z komory poprzez przewody transportujące urobek. W tylnej części urządzenia pomiędzy przewodem podającym płuczkę bentonitową do komory kruszenia, a przewodem transportującym urobek znajduje się obejście tzw. bajpas. Po zakończeniu wiercenia obejście to otwiera się, zamykając jednocześnie przepływ płuczki do komory kruszenia. Przepływ płuczki lub wody następuje wówczas przez przewody płuczkowe, a następnie poprzez obejście bezpośrednio do przewodów transportujących urobek, w celu wyczyszczenia przewodów z urobku.
W miejscu połączenia pierwszego modułu z drugim na obwodzie urządzenia rozmieszczone są siłowniki hydrauliczne. Poprzez ich wysunięcie (skrócenie lub wydłużenie) możliwe jest sterowanie urządzeniem, bowiem pierwszy moduł głowicy zamontowany jest przegubowo względem pozostałych.
W urządzeniach do mikrotunelowania o średnicy od 1200 mm wzwyż możliwy jest dostęp do tarczy urządzenia poprzez właz i śluzę powietrzną, w celu ewentualnej wymiany elementów skrawających.
Niektóre głowice, o większych średnicach, wyposażone są w systemy równoważenia parcia gruntu oraz wody gruntowej, w celu zapobieżenia tworzenia się kawern w gruncie oraz osuwania się gruntu w strefie przodka, a w dalszej konsekwencji naruszenia struktury powierzchni terenu. Systemy równoważenia parcia gruntu działają na zasadzie podawania do strefy urabiania gruntu płuczki bentonitowej pod odpowiednio dobranym ciśnieniem lub sprężonego powietrza.
Każde z produkowanych urządzeń do mikrotunelowania można użyć do wbudowania rurociągu o jednej średnicy, ewentualnie poprzez zastosowanie nakładki poszerzającej możliwe jest wbudowanie rurociągu o średnicy większej o jedną dymensję.
Na czym polega metoda HDD?
- Metoda HDD– polega na wykonywaniu poziomych przewiertów sterowanych (HDD – HorizontalDirectionalDrilling). Przewierty horyzontalne są odmianą otworów kierunkowych. Dzięki zastosowaniu nowoczesnych systemów pomiarowych i sterujących, trajektoria wykonanego przewiertu i położenie punktu wyjścia w sprzyjających warunkach wiertniczych mogą być bliskie z zaprojektowanymi, co pozwala na wykonywanie tego typu przewiertów na terenach silnie zurbanizowanych. Horyzontalny przewiert sterowany umożliwia układanie rurociągu pod przeszkodami takimi jak: kanały i rzeki. W przeciwieństwie do techniki wiercenia poziomego, która wymaga wstępnych wykopów po obu końcach przewiertu, horyzontalny przewiert sterowany można wykonać z poziomu gruntu, dzięki zakrzywianiu trajektorii przebiegu przewiertu.Podstawowym elementem przy planowaniu horyzontalnego przewiertu sterowanego jest ustalenie trajektorii pomiędzy dwoma punktami, punktem wejścia a punktem wyjścia. Z tego powodu wiele warunków musi zostać wziętych pod uwagę, aby teoretyczna trajektoria mogła być możliwa do zrealizowania w praktyce. Parametry otworu dobiera się na podstawie rodzaju oraz wielkości instalowanego rurociągu, badań geotechnicznych oraz jego wielkości docelowej. Średnica rurociągu oraz materiał, z jakiego jest wykonany są najistotniejszymi parametrami decydującymi o geometrii otworu oraz o jego wielkości docelowej.Przy realizacji trajektorii otworu podstawowymi parametrami są:
- kąt wejścia i kąt wyjścia
- głębokość posadowienia w sekcji poziomej
- łuki pionowe i poziome
- przykrycie
- „overcut” stosunek średnicy otworu do średnicy rurociągu
- wielkość otworu
Kąt wejścia jest to odchylenie planowanej trajektorii otworu w punkcie zetknięcia narzędzia wiercącego z gruntem odnoszone do poziomu.
Kąt wyjścia jest to kąt powstały pomiędzy żerdzią, a powierzchnią terenu w punkcie wyjścia. Podobnie jak kąt wejścia jest on zależny od średnicy i rodzaju instalowanego rurociągu. Należy także pamiętać o dostępnej przestrzeni i warunkach na ułożenie rurociągu do wciągania. Kąt wyjścia determinuje ułożenie rurociągu podczas etapu instalacji tzw. „overbend”. Podczas wciągania rurociągu do otworu, zanim przejdzie do sekcji prostoliniowej, najpierw rurociąg wykreśla łuk („overbend”).
Tylko niektóre rodzaje gruntów są nieodpowiednie do metody przewiertu HDD (głównie upłynniona forma gliny, a także formacje żwirów), a głowice wiertnicze dobierane są ściśle do rodzaju gruntu, poczynając od miękkich, kończąc na bardzo twardych skałach granitowych lub nawet bazaltowych.
Elementy systemu wiercącego:
- urządzenie wiertnicze
- system płuczkowy (przygotowanie, pompowanie, rozdział faz, kondycjowanie)
- przewód wiertniczy
- dolny zestaw przewodu
- system kierowanie trajektorią (nawigacja – lokalizacja)
Głowica wiertnicza wyposażona jest w głowicę rozwiercającą odpowiednią do danego rodzaju gruntu, dysze i sondę. Całość napędzana jest przez zestaw skręconych ze sobą stalowych elementów: żerdzi.
Proces wykonywania przewiertu składa się z kilku etapów:
- wiercenia pilotowego,
- poszerzenia otworu,
- oczyszczenia i kalibracji otworu,
- instalacji rurociągu
Zadaniem etapu pierwszego jest wykonanie przewiertu pilotażowego pod przeszkodą. Narzędzie wiercące jest prowadzone po wcześniej zaprojektowanej trajektorii przez wiertnicę. Siła pchania oraz moment obrotowy są przenoszony przez żerdzie wiertnicze do narzędzia wiercącego. Za świdrem skrawającym umieszczona jest żerdź, w której znajduje się sonda pomiarowa. Tak przygotowany zestaw wwierca się w grunt, systematycznie dokręcając żerdzie wiertnicze tworzony jest otwór wiertniczy. Płuczka wiertnicza, która najczęściej jest mieszaniną wodno – dyspersyjną, zawierająca w swoim składzie bentonit, jest pompowana przez żerdzie do dolnego zestawu przewodu w tym przypadku świdra skrawającego jak to zostało wspomniane powyżej i wypływa z niego pod dużym ciśnieniem z dyszy. Urabiany grunt jest transportowany na powierzchnię przestrzenią pierścieniową dzięki płuczce wiertniczej. Świder wiertniczy dobiera się w oparciu o warunki geologiczne, w których przebiegać ma wiercenie.
Kolejnym etapem przewiertu jest poszerzenie otworu pilotażowego w celu umożliwienia instalacji rury o zakładanej średnicy. Grunt urabiany jest przy pomocy poszerzaczy o średnicy większej o 20% – 50% od średnicy instalowanej w otworze rury w zależności od warunków geologicznych w miejscu wykonywania wiercenia. Urobek powstały na skutek zwiercania warstw jest transportowany z otworu przez płuczkę wiertniczą.
Finalny etap stanowi instalacja rury produktowej. W tym celu do instalowanej rury zostanie przyspawana głowica ciągnąca. Jest ona połączeniem między instalowanym rurociągiem a przewodem wiertniczym. Do głowicy przymocowany zostaje krętlik. Pozwala on na swobodny obrót przewodem wiertniczym wraz z narzędziem, a uniemożliwia kręcenie instalowanym rurociągiem. Dzięki temu na instalowany rurociąg przenoszona zostaje tylko siła ciągnięcia.
Średnica otworu wiertniczego zależy od średnicy instalowanego rurociągu, jak również od długości przewiertu, rodzaju gruntu, promienia łuku itp. Wiercenie wykonuje się wieloetapowo przeprowadzając rozwiercania pośrednie, stosując coraz większe narzędzia urabiające, w celu uzyskania optymalnej wielkości otworu, którego średnica musi zawierać się pomiędzy 1.2 – 1.5 średnicy rurociągu. Głowica rozwiercająca wyposażona jest w dysze, podobnie jak głowica wiertnicza. Dysze podają bentonit, który redukuje efekt nagrzewania i tarcia.
Na czym polega metoda Direct Pipe?
- Direct Pipe (DP) to nowoczesna, bezwykopowametoda instalacji rurociągów stalowych o średnicach – od 28” (Dz. 711 mm) do 60’’ (Dz. 1524 mm) pod przeszkodami terenowymi. Jest to metoda jednoetapowa, polegająca na tym, że jednocześnie z drążeniem otworu przy pomocy specjalnej głowicy mikrotunelowej wprowadzana jest docelowa rura przewodowa. Istotą tej technologii jest ograniczenie placu budowy do jednej, maszynowej strony roboczej, możliwość znacznego wypłycenia rurociągu, układanie rurociągów w każdych warunkach geologicznych i to wszystko przy zminimalizowanym ryzyku wykonawczym. Technologia Direct Pipe łączy zalety mikrotunelowania z metodą horyzontalnego przewiertu sterowanego (HDD). Aktualnie w Polsce metoda Direct Pipe jest stosowana podczas najtrudniejszych przekroczeń bezwykopowych.
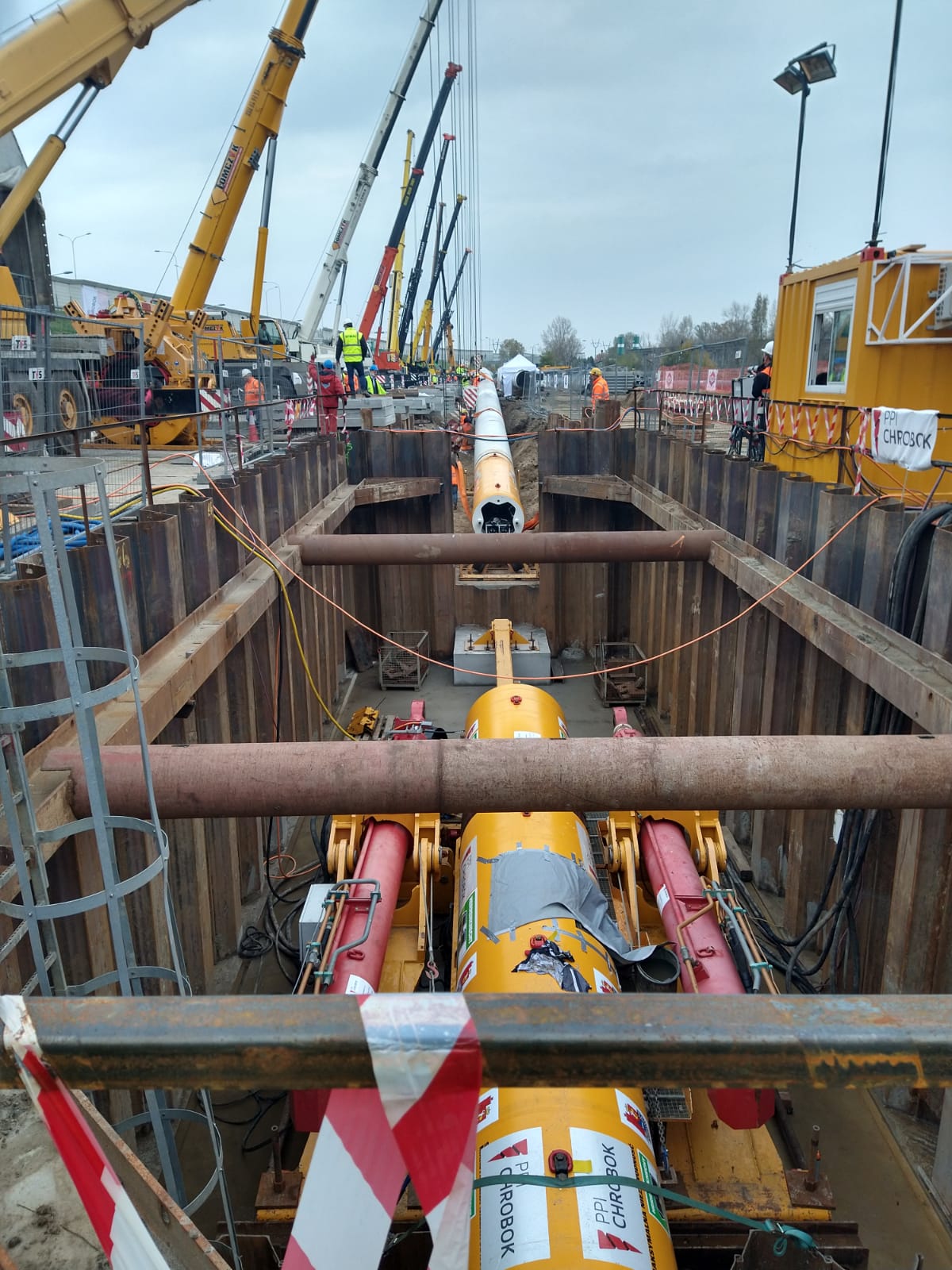
Jakie inne analizy wykonujemy w ramach przekroczeń bezwykopowych?
Wspieramy firmy wykonawcze w trudnych sytuacjach np. podczas awarii wymagających szybkiego i sprawnego zaprojektowania głębokich komór ratunkowych ze ścianek szczelnych. Wykonujemy także analizy wytrzymałościowe rur przewiertowych. Specjalizujemy się analizach wytrzymałościowych rurociągów w fazie instalacji (dot. technologii bezwykopowych) i eksploatacji dla trudnych przekroczeń bezwykopowych np. głębokie przekroczenia Direct Pipe czy mikrotunelowanie. Wykorzystujemy do tego modelowanie numeryczne metodą elementów skończonych (MES). Swoje usługi projektowe i doradcze świadczyliśmy na wielu strategicznych kontraktach np. BalticPipe, przekroczenie rzeki Wisły (Oczyszczalnia ścieków Czajka), polskie Elektrociepłownie.
Zapraszamy do kontaktu
Podanie danych w powyższym formularzu jest całkowicie dobrowolne, jednak niezbędne do prawidłowego przetworzenia Państwa zapytania. Uzupełniając powyższy formularz kontaktowy wyrażają Państwo zgodę na przetwarzanie danych osobowych zgodnie z Rozporządzeniem Parlamentu Europejskiego i Rady (UE) 2016/679 z dnia 27 kwietnia 2016 r.